Elektrohydraulische Servolenkung - Aufbau und Funktionsweise
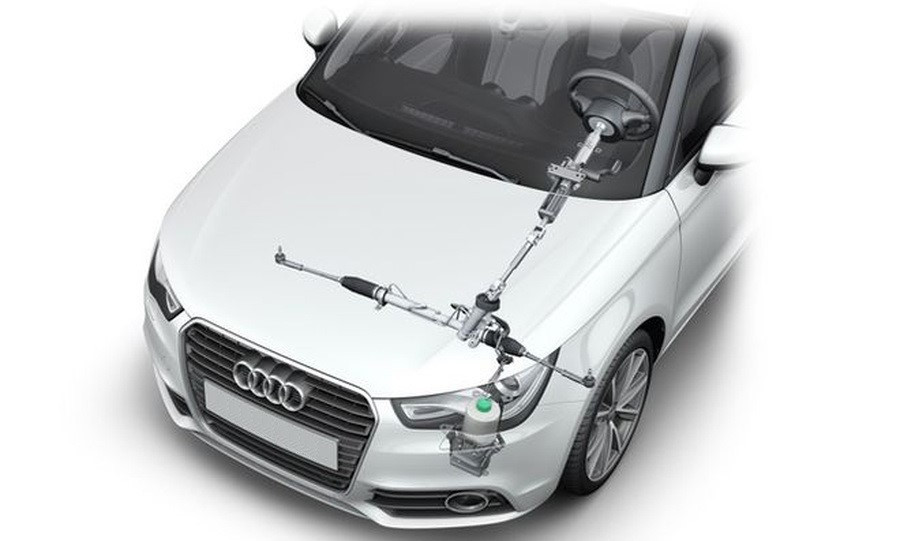
Die Konstruktion der Autolenkung wurde zusammen mit den anderen Komponenten ständig verbessert. Als die Geschwindigkeit und das Gewicht der Autos zunahmen, wurde die Frage der Servolenkung wichtig - die Muskeln des Fahrers waren nicht mehr in der Lage, das Manövrieren und Einparken zu bewältigen.
Die erste Servolenkung war eine hydraulische, die von einer Kurbelwelle über ein Riemengetriebe angetrieben wurde. Sie wird auch heute noch verwendet, weil sie zuverlässig und effizient ist, aber sie hat erhebliche Nachteile, vor allem die Abhängigkeit der Pumpenleistung von der Motordrehzahl und den ständigen Verbrauch von Energie zum Drehen der Hydraulikpumpe, auch wenn das Auto geradeaus fährt. Die Entwicklung des hydraulischen Boosters wurde eingeleitet.
Wie die elektrische Servolenkung entwickelt wurde
.
Die erste Stufe des variablen Hydrauliksystems war das Servotronic-Ventil, das den Druck in der Hydraulikleitung abbaute, wenn das Auto mit hoher Geschwindigkeit bewegt wurde. Die Lenkung wurde flexibler und reaktionsschneller, aber das war nur die Hälfte des Problems. Herkömmlich konzipierte Servolenkungen sind sehr schwer zu manövrieren, vor allem im Straßenverkehr, wenn maximale Leistung erforderlich ist, der Motor aber normalerweise mit minimaler Geschwindigkeit läuft. Die Konstrukteure mussten die Pumpe für maximale Leistung auslegen und überschüssige Arbeitsflüssigkeit bei hohen Motordrehzahlen über einen Bypass ablassen.
Außerdem löste die Servotronic nicht das Hauptproblem des Hydrauliksystems: die konstanten Drehzahlen beim Betrieb des Verbrennungsmotors und die damit verbundenen erheblichen Nachteile, wie
- erhöhter Kraftstoffverbrauch und Luftemissionen;
- schnellerer Verschleiß der Servolenkungspumpe und verminderte Flüssigkeitsqualität;
- das Vorhandensein eines Riemenantriebs und damit die Bindung an einen bestimmten Einbauort;
Da die Leistung der Kfz-Generatoren zunahm und die Elektronik sich verbesserte, wurde es möglich, die Hydraulikpumpe mit einem Elektromotor auszustatten. Zunächst handelte es sich um Kollektormotoren. Solche Pumpen waren noch nicht in der Lage, die Leistung zu verändern, aber da es keinen Antriebsriemen gab, konnte die Einheit überall im Motorraum installiert werden. Die Leistung der Pumpe war nicht mehr direkt von der Motordrehzahl abhängig. Später wurden sie mit einem Sanftanlaufsystem und dann mit einem Steuergerät für den hydraulischen Booster mit Diagnosemöglichkeiten ausgestattet.
Da es keine Beanstandungen über den Druckteil der Pumpen gab, der sich durch hohe Qualität und Leistung auszeichnet, wurden die Geräte durch die Entwicklung von elektrischen Antriebsmotoren weiter verbessert. Permanentmagnetische bürstenlose Elektromotoren (BLDC) wurden eingeführt. Im Folgenden werden alle Arten und Typen von Elektromotoren verglichen.
Aufbau und Funktionsweise eines elektrohydraulischen Verstärkers
Das Funktionsprinzip ist mit dem Aufkommen von Elektromotoren und der sie steuernden Elektronik praktisch unverändert geblieben. Nach wie vor wird die Lenkraddrehung des Fahrers durch den Druck der Arbeitsflüssigkeit verstärkt, allerdings wird dieser nun durch eine vom Verbrennungsmotor unabhängige Pumpe mit Elektroantrieb erzeugt. Lediglich das Drehkolbengehäuse verfügt über einen Servolenkungssensor, der Daten über die Lenkraddrehzahl an das elektronische Steuergerät übermittelt, damit dieses die Pumpendrehzahl anpassen kann.
Das hydraulische Servolenkungssystem umfasst:
- Pumpe
- Arbeitsflüssigkeitsdruckregler;
- Ausdehnungsgefäß;
- Steuerventil (Schieber);
- Lenkungszahnstange (oder Lenkgetriebe) mit einem Arbeitszylinder;
- Hoch- und Niederdruckschläuche.
Zusätzlich kann die Servolenkung einen Hydraulikölfilter und/oder -kühler enthalten.
Pumpenaufbau und Funktionsprinzip
Der Aufbau dieser Vorrichtung kann in zwei Teile unterteilt werden:
- Hydraulisch.
- Elektrisch.
Bei den meisten Autos sind sie zu einem einzigen Aggregat zusammengefasst. Diese besteht aus:
- Hydraulikmodul mit Zahnradpumpe und Reduzierventil;
- Elektromotor;
- Behälter für Arbeitsflüssigkeit;
- Steuergerät für die Servolenkung;
Die Pumpe ist über spezielle Ablassschläuche mit dem Lenkmechanismus verbunden. Wie bei einem herkömmlichen Hydrauliksystem ist die Ablassleitung mit dem Auffangbehälter verbunden. Im Motorraum ist die Pumpe an einer Konsole befestigt, die in der Regel mit elastischen Gummielementen an der Karosserie oder dem Rahmenträger befestigt ist.
Aufbau des hydraulischen Teils einer Servolenkungspumpe
Die pumpenden Komponenten von Servolenkungspumpen lassen sich in drei Typen unterteilen:
- Getriebegehäuse
- Kolben
- Schaufel
Die am häufigsten in modernen Autos eingebauten Pumpen sind vom ersten Typ. Der Grund dafür ist die relativ einfache Konstruktion, der hohe Wirkungsgrad und die hohe Leistung.
Die rotierenden Zahnräder saugen die Flüssigkeit in den Zahnzwischenraum und befördern sie von der Niederdruckzone in die Hochdruckzone, wodurch sie in das Netz gepresstób wird. Da es praktisch keinen Spalt zwischen dem Körper und den Enden der Zähne gibt, ist eine gute Abdichtung gewährleistet. Diese wird seitlich durch Platten oder Buchsen, die auch als Lager für die Zahnräder dienen, ergänzt und verstärkt.
Der hydraulische Teil der Pumpe ist wartungsfrei. Der hydraulische Teil der Pumpe erfordert keine Wartung. Seine Teile werden während des Betriebs mit Arbeitsflüssigkeit geschmiert.
Elektrischer Teil
Dazu gehören die Elektromotoren, die die Pumpe antreiben, und die Elektronik, die sie steuert. Je nach Fahrzeugmodell, Motortyp und anderen Faktoren kann es sich dabei um ein Steuergerät, einen Mikrocontroller oder ein Relais handeln. Es gibt eine Reihe von Möglichkeiten, die Pumpenelektronik zu steuern:
- Strom in die Klemme einspeisen (einfachste Art).
- Steuerung über ein Steuergerät.
- Steuerung durch Pulsweitenmodulation (PWM) auf Basis von Motordrehzahl- und Fahrzeuggeschwindigkeitssensoren.
- Über die K-Line-Diagnoseschnittstelle (verwendet bei frühen Generationen von EHPC-Geräten).
- Der CAN-Bus ist die modernste Methode, die bei Pumpen sowohl zur Steuerung als auch zur Diagnose verwendet wird.
Zwei Arten von Elektromotoren werden in elektrischen und elektrohydraulischen Servolenkungen eingesetzt:
- Kollektormotoren (Bürstenmotoren);
- Bürstenlose (BLDC) Motoren;
Kollektormotoren wurden früher eingebaut und haben eingeschränkte Funktionen. Sie können jedoch nicht eindeutig als minderwertig angesehen werden, da jeder dieser beiden Motortypen seine Vor- und Nachteile hat.
Bürstenverteilermotor
Vorteile:
- Einfache Herstellung und Wartung.
- Einfache Drehzahlregelung.
- Geringe Kosten im Vergleich zu BLDC.
Nachteile:
- Die Notwendigkeit der Wartung der Bürsten-Kollektor-Baugruppe.
- Geringes Drehmoment beim Anfahren.
- Geringerer Wirkungsgrad
Bürstenloser Motor (BLDC)
Vorteile:
- Hoher Wirkungsgrad und hohe Drehmomentwerte.
- Keine reibungs- und verschleißanfälligen Bürsten.
- Hohe Zuverlässigkeit und lange Lebensdauer.
- Möglichkeit der stufenlosen Einstellung der Pumpendrehzahl.
Schwächen:
- Hohe Kosten im Vergleich zu Bürstenómotoren durch die Verwendung von teuren Magneten.
- Aufwändigeres elektronisches Steuerungssystem.
Typische Fehler der elektrohydraulischen Servolenkung
Genauso wie die Teile des Pumpenaggregats lassen sich auch die Störungen des Aggregats in mechanische und elektrische einteilen. Die häufigsten der ersten Gruppe sind:
- Austritt von Arbeitsflüssigkeit durch gebrochene Dichtungen oder Beschädigung von Schläuchen und Rohren in der Hauptleitung;
- Verschmutzung des Druckminderventils;
- Verschleiß von Zahnrädern.
Im ersten Fall lassen sich Störungen an Ölflecken unter dem Auto erkennen, in den anderen Fällen an einem Druckabfall im System und einem schwergängigen Lenkrad.
Elektrische Pannen sind vielfältiger. Diese sind:
- Verschleiß oder Beschädigung von Teilen des Elektromotors: Bürsten, Wicklungen, Kollektor;
- Fehlfunktion der Elektronik: Steuerplatine, Feldeffekttransistoren;
- Fehlfunktion der Sensoren;
- Fehlende Kommunikation mit dem Steuergerät oder der Steuerplatine;
Häufige Ursachen sind Korrosion von Kontakten oder Teilen sowie Kurzschlüsse in Verbindung mit dem Eindringen von Betriebsflüssigkeit in die Elektronikeinheit.
Reparatur der elektrischen Servolenkung
Obwohl die Hersteller im Falle einer Fehlfunktion oft den Austausch der gesamten Einheit empfehlen, lassen sich die Pumpen der Servolenkung durchaus reparieren. Hauptsache, man wendet sich an qualifizierte Handwerker - zum Beispiel an die Firma STS, deren Spezialisten über die nötige Ausrüstung für die Reparatur sowie über langjährige Erfahrung in der Wartung und Instandsetzung von Lenkungen verfügen.