Elektrohydrauliczne wspomaganie układu kierowniczego - budowa i zasada działania
- Jak powstało elektryczne wspomaganie kierownicy
- Struktura i zasada działania wzmacniacza elektrohydraulicznego
- Konstrukcja i zasada działania pompy
- Struktura części hydraulicznej pompy wspomagania układu kierowniczego
- Część elektryczna
- Silnik bezszczotkowy (BLDC)
- Typowe usterki elektrohydraulicznego wspomagania kierownicy
- Naprawa elektrycznego wspomagania układu kierowniczego
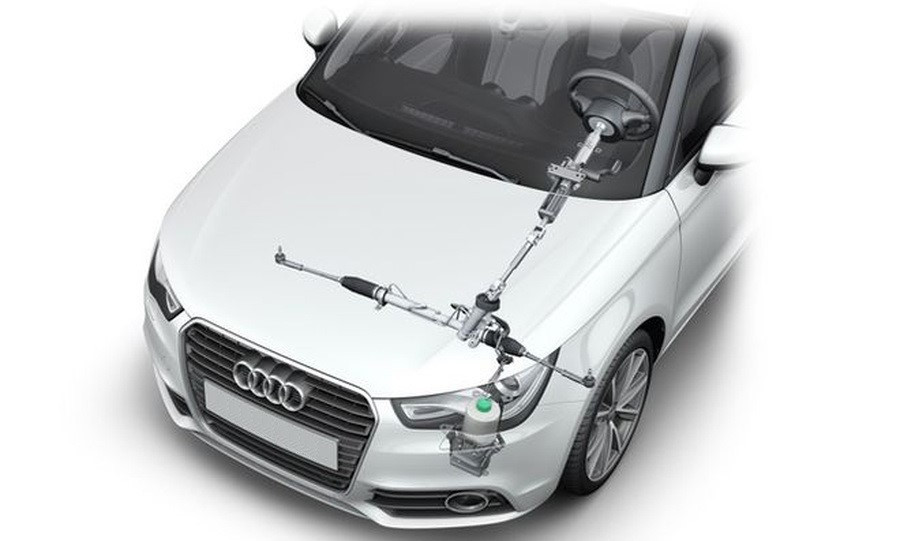
Konstrukcja układu kierowniczego samochodu była stale ulepszana wraz z innymi jego komponentami. Wraz ze wzrostem prędkości i masy samochodów, a także wzrostem ich liczby, kwestia wspomagania kierownicy stała się istotna - mięśnie kierowcy nie były już w stanie poradzić sobie z manewrowaniem i parkowaniem.
Pierwszy system wspomagania kierownicy był hydrauliczny, napędzany przez wał korbowy za pomocą przekładni pasowej. Jest on nadal używany, ponieważ jest niezawodny i wydajny, ale ma znaczące wady, z których główne to zależność wydajności pompy od prędkości obrotowej silnika i stałe zużycie części mocy na obracanie pompy hydraulicznej, nawet jeśli samochód jedzie w linii prostej. Ewolucja wzmacniacza hydraulicznego została zapoczątkowana.
Jak powstało elektryczne wspomaganie kierownicy
Początkowym etapem tworzenia układu hydraulicznego o zmiennych parametrach był zawór servotronic, który uwalniał ciśnienie w przewodzie hydraulicznym, gdy samochód poruszał się z dużą prędkością. Układ kierowniczy stał się bardziej elastyczny i responsywny, ale to była tylko połowa problemu. Tradycyjnie zaprojektowane układy wspomagania kierownicy mają duże trudności z manewrowaniem, zwłaszcza w ruchu, gdy wymagana jest maksymalna moc, ale silnik zwykle pracuje z minimalną prędkością. Projektanci musieli zaprojektować pompę dla maksymalnej mocy i odprowadzać nadmiar płynu roboczego przy wysokich prędkościach obrotowych wału silnika poprzez obejście.
Ponadto, servotronic nie rozwiązywał głównego problemu układu hydraulicznego: stałych obrotów podczas pracy silnika spalinowego i towarzyszących temu znaczących wad, takich jak
- zwiększone zużycie paliwa i emisja spalin do atmosfery;szybsze zużycie pompy wspomagania i obniżona jakość płynu;
- obecność napędu pasowego, a co za tym idzie, przywiązanie do konkretnego miejsca instalacji.
W związku z tym, wraz ze wzrostem mocy generatorów samochodowych i poprawą elektroniki, możliwe stało się wyposażenie pompy hydraulicznej w silnik elektryczny. Początkowo były to silniki typu kolektorowego. Takie pompy nie były jeszcze w stanie zmienić wydajności, ale dzięki brakowi paska napędowego jednostka mogła być zainstalowana w dowolnym miejscu w komorze silnika. Wydajność pompy nie zależała już bezpośrednio od prędkości obrotowej silnika. Później wyposażono je w system łagodnego rozruchu, a następnie w jednostkę sterującą wspomaganiem hydraulicznym z możliwościami diagnostycznymi.
Ponieważ nie było żadnych skarg na część tłoczną pomp, która charakteryzuje się wysoką jakością i wydajnością, dalsze udoskonalanie jednostek odbywało się poprzez rozwój elektrycznych silników napędowych. Wprowadzono bezszczotkowe silniki elektryczne z magnesami trwałymi (BLDC). Poniżej porównamy wszystkie rodzaje i typy silników elektrycznych.
Struktura i zasada działania wzmacniacza elektrohydraulicznego
Zasada działania tego pierwszego pozostała praktycznie niezmieniona wraz z pojawieniem się silników elektrycznych i sterującej nimi elektroniki. Obrót kierownicy nadal jest wzmacniany przez ciśnienie płynu roboczego, choć teraz jest on wytwarzany przez pompę z niezależnym napędem elektrycznym od silnika spalinowego. Tylko w korpusie obrotowej szpuli znajduje się czujnik wspomagania kierownicy, który przesyła dane o prędkości obrotowej kierownicy do elektronicznej jednostki sterującej, aby mogła ona dostosować prędkość pompy.
Hydrauliczny układ wspomagania kierownicy obejmuje:
- pompa;
- regulator ciśnienia płynu roboczego;
- zbiornik wyrównawczy;
- zawór sterujący (suwak);
Ponadto, filtr i/lub chłodnica płynu hydraulicznego mogą być dodatkowo zainstalowane w układzie wspomagania kierownicy.
Konstrukcja i zasada działania pompy
Konstrukcję tego urządzenia można podzielić na dwie części:
W większości samochodów są one połączone w jedną jednostkę. Składa się on z:
- moduł hydrauliczny z pompą zębatą i zaworem redukcyjnym;
- silnik elektryczny;
- zbiornik płynu roboczego;
- jednostka sterująca wspomaganiem układu kierowniczego.
Pompa jest połączona z mechanizmem kierowniczym za pomocą specjalnych węży spustowych. Podobnie jak w konwencjonalnym układzie hydraulicznym, przewód spustowy jest podłączony do zbiornika wyrównawczego. W komorze silnika pompa jest przymocowana do wspornika, który jest zwykle przymocowany do elementu nośnego nadwozia lub ramy za pomocą sprężystych elementów gumowych.
Struktura części hydraulicznej pompy wspomagania układu kierowniczego
Pomimo faktu, że elementy tłoczące pompy wspomagania układu kierowniczego można podzielić na trzy typy:
- przekładnia
- tłok
- łopatkowe,
najczęściej w nowoczesnych samochodach instalowane są pompy pierwszego typu. Powodem jest stosunkowo prosta konstrukcja, wysoka sprawność i wydajność.
Obracające się koła zębate zasysają płyn do przestrzeni między zębami i przenoszą go ze strefy niskiego ciśnienia do strefy wysokiego ciśnienia, wtłaczając go w ten sposób do sieci. Ponieważ praktycznie nie ma szczeliny między korpusem a końcówkami zębów, zapewnione jest dobre uszczelnienie. Jest ono uzupełnione i wzmocnione po bokach płytami lub tulejami, które działają również jako łożyska dla kół zębatych.
Część hydrauliczna pompy nie wymaga konserwacji. Jej części są smarowane płynem roboczym podczas pracy.
Część elektryczna
Obejmuje to silniki elektryczne napędzające pompę i elektronikę, która nimi steruje. W zależności od modelu pojazdu, typu silnika i innych czynników, może to być jednostka sterująca, mikrokontroler lub przekaźnik. Istnieje wiele sposobów sterowania elektroniką pompy:
- Podawanie prądu do zacisku (najprostszy typ).
- Sterowanie za pomocą modulacji szerokości impulsu (PWM) w oparciu o prędkość obrotową silnika i czujniki prędkości pojazdu.
- Poprzez interfejs diagnostyczny K-line (używany we wczesnych generacjach jednostek EHPC).
- Magistrala CAN jest najnowocześniejszą metodą stosowaną w pompach zarówno do sterowania, jak i diagnostyki.
W elektrycznych i elektrohydraulicznych układach wspomagania kierownicy stosowane są dwa rodzaje silników elektrycznych:
- Silniki kolektorowe (szczotkowe);
- silniki bezszczotkowe (BLDC).
Silniki kolektorowe były instalowane wcześniej i mają ograniczone funkcje. Nie można ich jednak uznać za jednoznacznie gorsze, ponieważ każdy z tych dwóch typów silników ma swoje wady i zalety.
Silnik z kolektorem szczotkowym
Zalety:
- Łatwość produkcji i konserwacji.
- Łatwość kontroli prędkości.
- Niski koszt w porównaniu do BLDC.
Wady:
- Konieczność konserwacji zespołu szczotka-kolektor.
- Niski moment obrotowy przy rozruchu.
- Niższa sprawność.
Silnik bezszczotkowy (BLDC)
Zalety:
- Wysoka wydajność i moment obrotowy.
- Brak szczotek narażonych na tarcie i zużycie.
- Wysoka niezawodność i długa żywotność.
- Możliwość płynnej regulacji prędkości pompy.
Słabe strony:
- Wysoki koszt w porównaniu do silników szczotkowych ze względu na zastosowanie drogich magnesów.
- Bardziej złożony elektroniczny system sterowania.
Typowe usterki elektrohydraulicznego wspomagania kierownicy
Podobnie jak w przypadku części jednostki pompującej, awarie jednostki można podzielić na mechaniczne i elektryczne. Z pierwszej grupy najczęstsze są
- wyciek płynu roboczego spowodowany awarią uszczelnienia lub uszkodzeniem węży i rur w linii;
- zanieczyszczenie zaworu redukującego ciśnienie
- zużycie kół zębatych.
W pierwszym przypadku usterki można rozpoznać po plamach oleju pod samochodem, a w pozostałych po spadku ciśnienia w układzie i zaciśniętej kierownicy.
Awarie elektryczne są bardziej zróżnicowane. Są to:
- zużycie lub uszkodzenie części silnika elektrycznego: szczotek, uzwojeń, kolektora;
- awaria elektroniki: płyta sterująca, tranzystory polowe;
- Awaria czujników;
- Brak komunikacji z jednostką sterującą lub płytą sterującą.
Częstymi przyczynami są korozja styków lub części, a także zwarcia związane z przenikaniem płynu roboczego do jednostki elektronicznej.
Naprawa elektrycznego wspomagania układu kierowniczego
Chociaż producenci często zalecają wymianę całego urządzenia w przypadku awarii, pompy układu wspomagania kierownicy można naprawić. Najważniejsze jest skorzystanie z pomocy wykwalifikowanych rzemieślników - na przykład firmy STS, której specjaliści posiadają cały niezbędny sprzęt do naprawy, a także wieloletnie doświadczenie w serwisowaniu i przywracaniu wszelkich układów kierowniczych.
- Jak powstało elektryczne wspomaganie kierownicy
- Struktura i zasada działania wzmacniacza elektrohydraulicznego
- Konstrukcja i zasada działania pompy
- Struktura części hydraulicznej pompy wspomagania układu kierowniczego
- Część elektryczna
- Silnik bezszczotkowy (BLDC)
- Typowe usterki elektrohydraulicznego wspomagania kierownicy
- Naprawa elektrycznego wspomagania układu kierowniczego