Direction assistée électro-hydraulique - construction et principe de fonctionnement
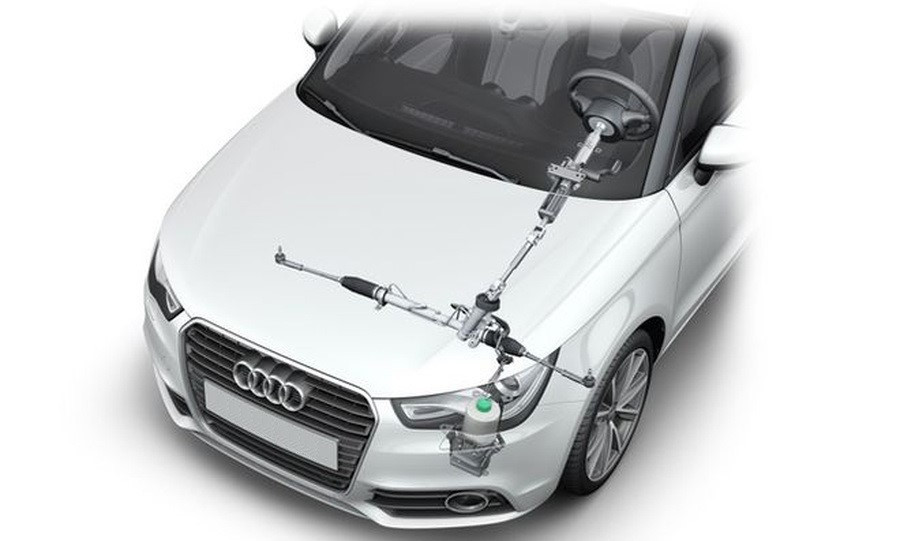
La conception du système de direction d'une voiture a été continuellement améliorée, de même que ses autres composants. Avec l'augmentation de la vitesse et du poids des voitures, ainsi que de leur nombre, la question de la direction assistée est devenue plus urgente : les muscles du conducteur ne pouvaient plus faire face aux manœuvres et au stationnement.
La première direction assistée était hydraulique, entraînée par le vilebrequin au moyen d'une courroie. Il est encore utilisé aujourd'hui parce qu'il est fiable et efficace, mais il présente des inconvénients importants, dont les principaux sont la dépendance du rendement de la pompe au régime du moteur et la consommation constante d'une partie de sa puissance pour faire tourner la pompe hydraulique, même si la voiture roule en ligne droite. L'évolution du système de direction assistée était imminente.
La première étape de la création d'un système hydraulique variable a été une valve servotronique qui relâchait la pression dans la conduite hydraulique lorsque la voiture roulait à grande vitesse. La direction est devenue plus élastique et plus réactive, mais ce n'était que la moitié du problème. Les systèmes de direction assistée de conception traditionnelle ont beaucoup de mal à manœuvrer, en particulier sur la route, lorsqu'une direction assistée maximale est requise alors que le moteur tourne généralement à une vitesse minimale. Les concepteurs ont dû concevoir la pompe pour une puissance maximale et évacuer l'excès de liquide de travail à des vitesses élevées de l'arbre du moteur par le biais d'une dérivation.
En outre, le servotronic ne résolvait pas le principal problème du système hydraulique : la rotation constante pendant le fonctionnement du moteur à combustion interne et les inconvénients importants qui l'accompagnent, tels que
- l'augmentation de la consommation de carburant et des émissions atmosphériques
- l'usure plus rapide de la pompe de surpression et la diminution de la qualité du fluide ;
- la présence d'une transmission par courroie, ce qui signifie qu'elle est liée à un emplacement d'installation spécifique.
C'est pourquoi, avec l'augmentation de la puissance des générateurs automobiles et l'amélioration de l'électronique, il est devenu possible d'équiper la pompe hydraulique d'un moteur électrique. Au départ, il s'agissait de moteurs à collecteur. Ces pompes n'étaient pas encore en mesure de modifier leurs performances, mais grâce à l'absence de courroie d'entraînement, l'unité pouvait être installée n'importe où dans le compartiment moteur. Les performances de la pompe ne dépendaient plus directement du régime moteur. Plus tard, elles ont été équipées d'un système de démarrage progressif, puis d'une unité de contrôle de diagnostic pour le surpresseur hydraulique.
Étant donné que la partie refoulement des pompes n'a fait l'objet d'aucune réclamation, car elle est de haute qualité et performante, les unités ont été améliorées en développant des moteurs d'entraînement électriques. Les moteurs électriques sans balais à aimant permanent (BLDC) ont été introduits. Nous allons comparer tous les types de moteurs électriques ci-dessous.
Structure et principe de fonctionnement de l'amplificateur électrohydraulique
Le principe de fonctionnement du premier est resté pratiquement inchangé avec l'avènement des moteurs électriques et de l'électronique qui les contrôle. Comme auparavant, la rotation du volant est amplifiée par la pression du fluide de travail, bien qu'elle soit désormais créée par une pompe dotée d'un entraînement électrique indépendant du moteur à combustion interne. Seul le boîtier du tiroir rotatif est désormais équipé d'un capteur de direction assistée qui transmet la vitesse du volant à l'unité de contrôle électronique afin qu'elle puisse ajuster la vitesse de la pompe.
Le système de direction assistée hydraulique se compose
- une pompe
- un régulateur de pression du liquide de travail
- un réservoir d'expansion
- une soupape de commande (tiroir) ;
- une crémaillère de direction (ou un boîtier de direction) avec un vérin ;
- des tuyaux haute et basse pression.
En outre, le système de direction assistée peut être équipé d'un filtre à fluide hydraulique et/ou d'un refroidisseur.
Conception et fonctionnement de la pompe
La conception de cette unité peut être divisée en deux parties :
- Hydraulique.
- Électrique.
Dans la plupart des voitures, ils sont combinés en une seule unité. Il s'agit de :
- module hydraulique avec pompe à engrenages et soupape de réduction;
- moteur électrique;
- Réservoir pour le fluide de travail;
- Unité de commande de la direction assistée;
La pompe est reliée au boîtier de direction par des tuyaux de refoulement spéciaux. Comme dans un système hydraulique conventionnel, la conduite de vidange est reliée au vase d'expansion. Dans le compartiment moteur, la pompe est fixée à un support, qui est généralement monté sur un élément moteur de la carrosserie ou du châssis, à l'aide d'éléments élastiques en caoutchouc.
Structure de la partie hydraulique de la pompe de suralimentation
Les éléments de refoulement des pompes de direction assistée peuvent être divisés en trois types :
- engrenage
- piston
- à palettes,
le plus souvent, les pompes du premier type sont installées dans les voitures modernes. La raison en est une conception relativement simple, une efficacité et des performances élevées.
Les engrenages rotatifs en prise aspirent le fluide dans l'espace entre les dents et le transfèrent de la zone de basse pression à la zone de haute pression, le forçant ainsi à s'écouler dans le réseau. Comme il n'y a pratiquement pas d'espace entre le corps et le sommet des dents, une bonne étanchéité est assurée. Elle est complétée et renforcée sur les côtés par des plaques ou des bagues qui servent également de paliers aux engrenages.
La partie hydraulique du groupe de pompage ne nécessite aucun entretien. Ses pièces sont lubrifiées par le fluide de travail pendant le fonctionnement.
Partie électrique
Il s'agit des moteurs électriques qui entraînent la pompe et de l'électronique qui les contrôle. En fonction du modèle de véhicule, du type de moteur et d'autres facteurs, il peut s'agir d'une unité de commande, d'un microcontrôleur ou d'un relais. Il existe plusieurs façons de contrôler l'électronique de la pompe :
- L'alimentation en courant de la borne (le type le plus simple).
- Commande par modulation de largeur d'impulsion (PWM) basée sur les capteurs de vitesse du moteur et du véhicule.
- Par l'intermédiaire de l'interface de diagnostic K-line (utilisée dans les premières générations d'unités EHPC).
- Le bus CAN est la méthode la plus moderne utilisée dans les pompes pour le contrôle et le diagnostic.
Deux types de moteurs électriques sont utilisés dans les directions assistées électriques et électrohydrauliques :
- Les moteurs à collecteur (à balais) ;
- les moteurs sans balais (BLDC).
Les moteurs à collecteur ont été installés plus tôt et sont limités dans certaines fonctions. Cependant, ils ne peuvent pas être considérés comme moins bons sans équivoque, car chacun des deux types de moteurs a ses avantages et ses inconvénients.
Moteur à collecteur à balais
Avantages:
Les avantages sont les suivants
- Facile à fabriquer et à entretenir.
- Contrôle facile de la vitesse.
- Faible coût par rapport à la BLDC.
Inconvénients:
- Maintenance de l'ensemble balai-collecteur.
- Faible couple au démarrage.
- Baisse de rendement.
Moteur sans balais (BLDC)
Avantages:
- Haute efficacité et valeurs de couple élevées.
- Pas de brosses sujettes à la friction et à l'usure.
- Haute fiabilité et longue durée de vie.
- Possibilité de réglage en douceur de la vitesse de rotation de la pompe.
Faiblesses:
- Coût élevé par rapport aux moteurs à balaisóen raison de l'utilisation d'aimants coûteux.
- Système de contrôle électronique plus complexe.
Défauts typiques de la direction assistée électrohydraulique
Tout comme les pièces de l'unité de pompage, les pannes de l'unité peuvent être divisées en mécanique et en électrique. Les plus courantes du premier groupe sont :
- fuite du fluide de travail due à la rupture des joints ou à l'endommagement des tuyaux et des conduites dans la ligne principale;
- contamination du détendeur de pression;
- usure des engrenages.
Dans le premier cas, les pannes peuvent être identifiées par des taches d'huile sous la voiture, et dans les autres cas par une baisse de pression du système et un volant tendu.
Les pannes électriques sont plus variées. Il s'agit de
- usure ou détérioration des pièces du moteur électrique : balais, enroulements, collecteur ;
- dysfonctionnement de l'électronique : carte de contrôle, transistors à effet de champ ;
- Dysfonctionnement des capteurs ;
- Absence de communication avec l'unité de contrôle ou la carte de contrôle.
Les causes fréquentes sont la corrosion des contacts ou des pièces, ainsi que les courts-circuits liés à la pénétration d'un fluide de travail dans l'unité électronique.
Réparation de la direction assistée électrique
Bien que les constructeurs recommandent souvent de remplacer l'ensemble du dispositif en cas de dysfonctionnement, les pompes du système de direction assistée sont tout à fait réparables. L'essentiel est de faire appel à des artisans qualifiés - par exemple, STS, dont les spécialistes disposent de tout l'équipement nécessaire à la réparation, ainsi que de nombreuses années d'expérience dans l'entretien et la restauration de tous les systèmes de direction.